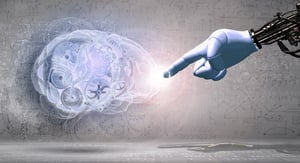
As Casa Sauza's director, I can see the imminent trend of the automation of processes in order to add value to our products. When implementing it, one must evaluate the difference between manual and artisan labor, in order to take it into progressive stages. Discover how we have managed to do it at Casa Sauza®.
The progress of the automation process can be analyzed from several angles. In this case, it will be analyzed from the perspective of the automation of the tasks that add direct value to the product. The labeling of the bottles will be taken as an example. The progress of the automation of the industry begins from a totally manual work to a fully automated work.
Difference between manual and artisan labor.
The labeling of a bottle by hand is manual work, not artisan/crafts. Unfortunately, these both terms are usually applied as if they meant the same thing, which they don't.
According to the RAE, artisan work is made by artisans, and describes an artisan as a person who exercises a merely mechanical art or trade. Or in these modern days, whoever makes household objects on their own and gives them their own personal touch, unlike factory workers.
The similarity between an artisan and a factory worker is that both of them work in a mechanical way. The difference is that the artisan works on its own and gives the product a personal/particular touch while the factory worker does it with and for a company, by series, and does not give the product any personal touch.
The labeling in a serial way on behalf of the company is a routine, repetitive and implies a physical effort, but is not artisan work.
Having made this distinction, we will now talk about the process from the manual labor of labeling bottles to the automation of the whole process, which also includes the quality guarantee of the product.
Automation of a Manual Process
The matter will be approached from the Technological Change and Continuous Improvement point of view, as well as from its implication in the transformation of the people that carry out the job.
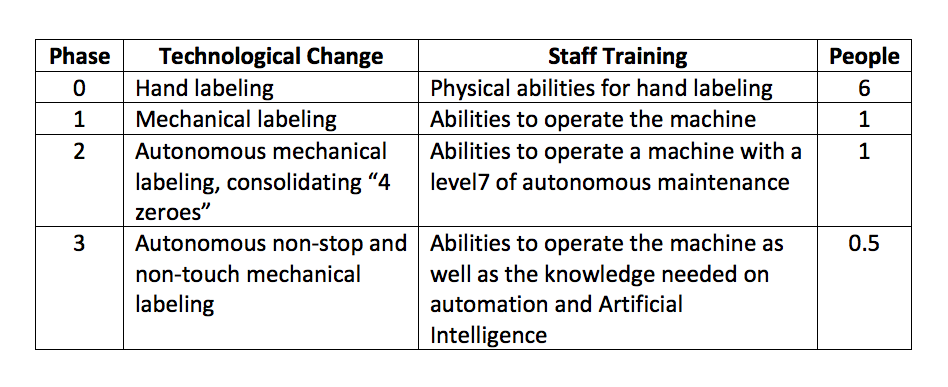
- On Phase 0, the job is done 100% manually
- On Phase 1, the operator only operates the machinery
- On Phase 2, The operator not only operates the machine but is responsible for the safety (zero accidents), maintenance (zero breakdowns) and efficiency (zero production decreases) of the equipment, as well as of the quality of the product (zero defects). All of this, with the support of the subsystems implemented for the company's TPM.
- On Phase 3, the operator not only operates the equipment and is held responsible for the 4 zeros (accidents, breakdowns, production decreases and defects) of the equipment but also suggests and carries out major improvements in order to achieve a non-stop production. He also has to improve in terms of getting it to not be operated by humans (non-touch), therefore, he must eventually find a way to get rid of tools, adjustments and inspections in such a way, that no operational abilities are needed for the operation of the equipment.
I will talk more about this interesting yet controversial issue on my following articles. Keep reading our Tequila Production Process blog in order to find out more about Casa Sauza's administration and production processes.
You can also come and visit Casa Sauza and see it all for yourself!