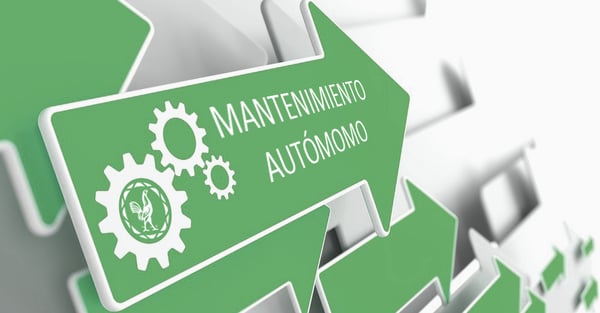
As an Agronomist, and throughout the more than 11 years of experience I have producing of tequila, more specifically in the application of the TPM methodology in the Tequila Industry, one of the most frequent questions that specialized visitors ask is: Why apply TPM? The answer is, to achieve a better working culture, as well as for the results and benefits that it brings to the factory.
Step 4 of Autonomous Maintenance is a stage of maximum usefulness for the development of our TPM. It allows us to develop abilities to better inspect our equipment in a systematic way so we can reassure the availability of our machinery by means of a zero breakdowns program.
An autonomous person is the one who knows how and can stand on its own, which something that the industry 4.0 requires in order to maintain the productivity and reliability of the equipment. This is why a good implementation of the Step 4: General Inspection, becomes indispensable.
The first 3 steps of TPM, previous to the implementation of step 4, are:
-
- Initial cleaning
- Elimination of contamination sources and of difficult access areas
- Elaboration of provisional standards for the inspection, cleaning, lubrication and tightening of the equipment.
This steps are carried out in order to avoid deterioration and to better control the basic conditions required for the maintenance of the equipment: cleanliness, tightening, lubrication and inspection.
Step 4 of TPM: General Inspection of Autonomous Maintenance
At step 4, we try to assess the deterioration of our equipment by carrying out a general inspection of it. By doing so, we not only improve the state of our equipment but also, when the operator works along with the mechanic at restoring the equipment to its best conditions, they each increase their competence and abilities related to the it.
Initially, the TPM team gives training on the inspection areas that need to be considered during the inspection:
- Mechanical
- Electrical
- Lubrication
- Pneumatic
- Hydraulic.
The TPM team makes use of a general inspection manual, which is previously prepared both by the staff and the supervisors.
The groups of workers participate in the elaboration of a failure mode matrix in order to identify and recognize the problem areas that were discovered during the maintenance inspection. Afterwards, the whole group takes the necessary actions in order to correct deterioration and improve the affected areas.
The general inspection training must be done for each area and comply with the training, application, audit, and modification cycles, which are repeated on each inspection area.
This step requires a long time to be completed, because all of the operators must develop the abilities needed to detect anomalies. In this step, we want our operators to increase their level of competition so, if we rush time, we would not consolidate them as competent, prepared and ready for the next steps that need to be taken. In other words, we would not have achieved the operator's autonomy, which is one of our main purposes.
The goal of this step is to improve the availability of the equipment (life cycle) by performing general inspections in order to prevent forced deterioration on each of the parts of the machine. The purpose is to understand the structure, functions and principles of the equipment by means of training each area.
Once the implementation of the Step 4 is done, it'll show in the LALI VR 4 Standard, with which we can visualize all the areas of our equipment.
For each area of our equipment we must have as a deliverable:
- Operating principle
- Carding, list of abnormalities and abnormalities OPL
- Flowchart
- Machine Tree
- Inspection sheet.
- Know Why sheet.
- Breakdown by area.
- KPI, breakdowns, minor stoppages, accidents, re-works.
At the end of Step 4, the company should be able to see significative changes and improvements, such as:
- Significant reduction of equipment failures
- Maturity in the operator
All of this will bring as a visible result, that the solutions to the abnormalities of the equipments that the mechanic used to provide, will be given by the operator instead, thanks to the training and the transference of abilities that took place.
If you would like to know more about tequila production processes carried out at Casa Sauza, you can keep reading our blog posts or you can also come and see it for yourself. Take one of our guided tours and learn from our experts, while you also visit Tequila, a Mexican Magical Town.