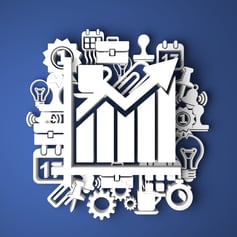
These days there are many different tools and methodologies that help us to simplify our processes and operative activities, commonly focused on the machines and equipment we use. On the other hand, some of these tools significantly impact the quality of life of the employees, causing an emotional maladjustment, health problems, stress, frustration, and even creating a hostile work environment.
According to the World Health Organization (WHO), the work stress causes the 25% of the 75,000 heart attacks per year, registered in Mexico; till now, the 75% percent of the Mexican workers suffer from this disease, which positions the country in the first place at a worldwide level, informed the Executive Secretary of the Comisión de Economía in San Lázaro, Jesús Valdés Palazuelos” (Source: "El Universal).
To improve the quality of life of its employees, Tequila Sauza is working in order to simplify the administrative processes to be able to reduce, eliminate, simplify, and automatize all the activities that in an administrative way, consume resources and time.
High Rotation Materials
The high rotation materials are the ones that, as their name indicates, are regularly used in the processes and they normally appear in all the inventories. There is a wide range of articles that have unique shapes, colors, brands, costs, etc. Some of them, even if they look insignificant due to its size, are very important in the production process, and not having them ready and on time, may cause accidents, safety incidents or equipment flaws.
In order to have a standard control of these consumables, it is necessary to have a record, files, and purchase receipts to administrate the inventory. Through these storage controls, the people in charge of the administration, manage the requirements of the purchase to supply their needs. However, it may happen that despite having this control, certain supplies could be missing and turn into urgent needs that may cause additional costs due to the needed airfreights to dispose the material on time. All of this urgent procedures have as a consequence a stress increase in the employees and in the processes.
The strategic supply area is the one interested in the optimization of resources and in the automatization of processes to reduce and eliminate the activities that don't add any value to the work. It is also important to analyze de internal supply process to detect possible flaws that may cause a lack of disponibility in the high rotation materials:
- Consumptions on time
- Appropriate Material Supply
- Appropriate Notifications of the Materials Re-Supply
- Reliable Inventories
Consumptions on time
It is vital that all the inputs and outputs of the materials are registered in the appropriately and correctly because if one of them is missing, this lack will be reflected in the inventory levels.
Appropriate Material Supply
It is important to work close to our providers and help them to develop skills in order to work together and make the process and the service grow. It is very beneficial to have all the inputs and outputs updated, to properly satisfy the company demands.
Appropriate Notifications of the Materials Re-Supply
In order for the providers to deliver the missing consumables on time, it is first necessary that the supply area has knowledge or those needs, and that is why the communication among the buyer and the supplier is recommended to be clear, precise, and mostly, on time.
Reliable Inventories
The accuracy of the inventories is of vital importance in this process, that is why is necessary that the suppliers elaborate cyclic inventories and keep them updated, in order to confirm the inputs and outputs and verifying that they are on time, detecting any possible difference or fault.
When considering all these variables in Casa Sauza, we explored different techniques, methods, mechanisms, and platforms, looking for the better option to implement, that could help us to concentrate the variables, analyze them and reduce the re-doing and the information loss. Thanks to the wits and creativity of the Purchase Manager (Jose Alberto Arizaga), a new platform was developed, this platform works using the internet and its called a Never Red Light (NRL) which uses a KANBAN system in our storage rooms.
By using this system we were able to define strategically all the minimum and maximum inventories, and all the information surrounding each component. Inside the NRL system, the restrictive data are stored, for example, the Inventory Levels, Material Existence, and Providers. The purchaser updates the inventories at a massive scale twice a week, and by doing so they are willing to detect the supply needs creating a report with the list of the materials. It is important to mention that we assign a yellow color to the missing pieces of the inventory that are at a minimum level, and red color when they are at a critic missing level in the inventories.
This system helps us to inform on a daily basis through e-mail to the providers in charge of the supplies, describing the missing pieces properly and avoiding the inventory to reach a 0 scale. By implementing all of these, Casa Sauza and the suppliers are able to have a better utilization of the materials and the time, because of an effective and direct communication. The providers are capable of seeing in the platform what are the needs of Casa Sauza, and deliver them as soon as possible.
If you want to know more about the Processes Simplification in Casa Sauza, read the following articles and feel free to contact us if you have any doubt!
Administrative Simplification in Casa Sauza
Applying Planned Maintenance in the Simplification of Processes