In the 19 years that I have been working in the bottling area at Casa Sauza ®, I have realized that some of the main problems that we face in this area are: the un-safety that some of our equipment presents, the wearing out of our machinery, the downtime generated by breakdowns and equipment failures, just to name a few.
During this time, I have been part of the implementation of some methodologies that sought to solve these problems but that never quite offered the results we were expecting. So it was after many tryouts and methodologies that we finally arrived to the one that has solved most of our problems in this area: The implementation of the TPM* Focused Improvement Pillar. (*Total Productive Maintenance).
Focused Improvement
Focused improvement includes activities that are developed by inter-functional teams or individually. Their goal is to maximize the effectivity of the equipment and decrease the company's losses and waste.
TPM techniques help to dramatically decrease the losses caused by equipment failures and guarantee their optimal functioning.
TPM Focused Improvement Pillar is one of the 7 TPM pillars
Focused Improvement tools that complement TPM
In order to carry out the optimization of our equipment, we use different techniques or tools that help us solve problems or make our processes easy and simple.
Just to mention some of them, we have:
- Poka Yokes (Quality technique used to avoid mistakes)
- Infinity Cycle (Mistake of carrying out a never-ending cycle)
- PM Analysis (Analysis to identify the determining force in a phenomenon)
- Makigami (Analysis of the work structure by using paper)
- 6 gens (Tool to return the equipment to basic conditions)
- 12 steps
- SMED (Single Minute Exchange of Die)
- Non Stop
- 5 W + 1 H (Tool that helps naming a problem)
In this article, I would like to focus my attention on one of the most useful tools of the Focused Improvement Pillar:
Finding what the problem is with the 5W + 1H technique
Sometimes, and I speak from my experience, when one doesn't truly know a problem, the easiest thing to do is to start guessing, and by doing so, we draw our attention from the real problem.
This easy technique guides us to identify the real problem by means of asking questions. It is used to understand and deepen on the situation that is being analyzed and know the circumstances and fundamental facts that belong to a problem.
Ask the following questions:
- What? Identify the events or actions that have taken place. What is the problem? What is happening?
- When? Identify all the time factors of what has happened (Time of the day or even the season when the problem appears) When does it happen?
- Where? Identify the conflict zone (whether it is an actual physical location in the plant or on the work process that it is related to) Where is the problem happening?
- Who? Identify the people involved (People of your organization, suppliers, clients or visitors that are part of the situation that must be solved) Who participates in this problem?
- How? Identify the way in which the events have ocurred. How does the problem happen?
- Why? Identify the causes of the events that have happened. Why is the problem happening?
- Problem. By answering each of the questions above we can better describe the problem, placing each answer as a sequence:
Problem= What?+ When?+ Where?+ Who?+ How?+ Why?
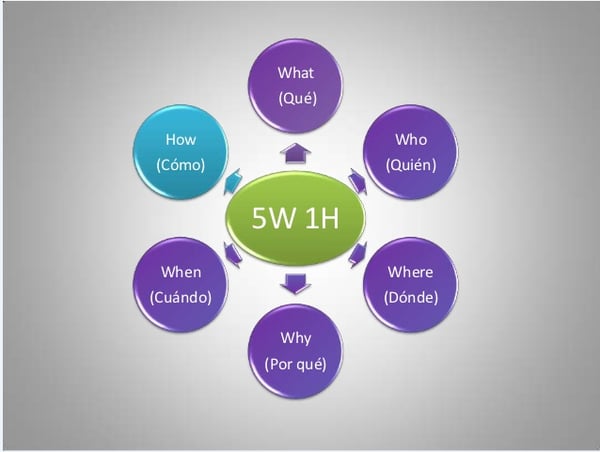
Come and visit Casa Sauza so you can learn how the modernization of our production processes deliver the purest tequila that you will find in the market.